We give the best Services
Health and Safety Management services are essential in the mining industry to ensure the well-being of workers, contractors, and surrounding communities. These services encompass a comprehensive approach to identifying, assessing, and mitigating health and safety risks associated with mining operations. Here is a detailed explanation of Health and Safety Management services:
1. Objective and Scope
Health and Safety Management services aim to prevent accidents, injuries, and occupational illnesses by creating a safe working environment. This involves implementing policies, procedures, and practices that protect all stakeholders involved in mining activities.
2. Health and Safety Policies
a. Policy Development
– Health and Safety Policies: Developing comprehensive health and safety policies that comply with local, national, and international regulations and standards.
– Commitment Statements: Creating statements that reflect the company’s commitment to health and safety.
b. Safety Culture
– Promoting Safety Culture: Fostering a culture of safety where employees at all levels prioritize health and safety in their daily activities.
– Leadership Commitment: Ensuring that leadership demonstrates commitment to health and safety through actions and resource allocation.
3. Risk Assessment and Management
a. Hazard Identification
– Workplace Inspections: Conducting regular inspections to identify potential hazards in the workplace.
– Job Safety Analysis (JSA): Analyzing specific job tasks to identify hazards and implement control measures.
b. Risk Assessment
– Risk Analysis: Assessing the likelihood and severity of identified hazards.
– Risk Control Measures: Implementing measures to eliminate or minimize risks, such as engineering controls, administrative controls, and personal protective equipment (PPE).
4. Health and Safety Programs
a. Occupational Health Programs
– Medical Examinations: Conducting pre-employment, periodic, and exit medical examinations to monitor workers’ health.
– Health Surveillance: Implementing health surveillance programs to detect early signs of work-related illnesses.
b. Safety Programs
– Safety Training: Providing regular training on safety procedures, emergency response, first aid, and the proper use of PPE.
– Safety Drills: Conducting emergency drills to prepare workers for potential incidents such as fires, explosions, or evacuations.
5. Workplace Safety Procedures
a. Standard Operating Procedures (SOPs)
– Development of SOPs: Creating detailed SOPs for all high-risk activities, ensuring they include safety protocols and emergency procedures.
– Compliance Monitoring: Regularly reviewing and updating SOPs to ensure compliance with current regulations and best practices.
b. Emergency Preparedness
– Emergency Response Plans: Developing and maintaining emergency response plans for various scenarios, including fires, chemical spills, and natural disasters.
– Crisis Management: Establishing crisis management teams and communication plans to manage emergencies effectively.
6. Incident Reporting and Investigation
a. Incident Reporting
– Reporting Systems: Implementing systems for reporting accidents, near-misses, and unsafe conditions.
– Encouraging Reporting: Creating an environment where employees feel comfortable reporting incidents without fear of retribution.
b. Incident Investigation
– Root Cause Analysis: Conducting thorough investigations of incidents to determine root causes.
– Corrective Actions: Implementing corrective actions to prevent recurrence of similar incidents.
7. Monitoring and Evaluation
a. Health and Safety Audits
– Internal Audits: Performing regular internal audits to assess compliance with health and safety policies and procedures.
– External Audits: Engaging third-party auditors to provide an objective assessment of health and safety performance.
b. Performance Metrics
– Tracking Metrics: Monitoring key performance indicators (KPIs) such as accident rates, lost-time injuries, and incident frequency rates.
– Continuous Improvement: Using data from audits and metrics to continuously improve health and safety practices.
8. Worker Participation and Consultation
a. Safety Committees
– Establishing Committees: Forming health and safety committees with representatives from different levels of the organization.
– Regular Meetings: Holding regular meetings to discuss safety concerns, review incidents, and propose improvements.
b. Employee Involvement
– Encouraging Participation: Involving employees in safety initiatives, hazard identification, and risk assessments.
– Feedback Mechanisms: Providing channels for employees to give feedback and suggestions on health and safety matters.
9. Compliance and Legal Requirements
a. Regulatory Compliance
– Compliance Monitoring: Ensuring that all health and safety practices comply with local, national, and international regulations.
– Regulatory Reporting: Submitting required reports to regulatory authorities and maintaining records of compliance.
b. Certification and Standards
– Achieving Certifications: Obtaining certifications such as ISO 45001 (Occupational Health and Safety Management Systems) to demonstrate commitment to high standards of health and safety.
10. Community Health and Safety
a. Community Risk Management
– Impact Assessments: Conducting health and safety impact assessments on surrounding communities.
– Engagement and Communication: Engaging with local communities to inform them about potential health and safety risks and the measures taken to mitigate them.
b. Public Health Initiatives
– Health Programs: Supporting public health programs in local communities, such as vaccination campaigns and disease prevention initiatives.
In summary, Health and Safety Management services are crucial for ensuring the safety and well-being of workers, contractors, and communities in the mining industry. These services encompass a wide range of activities, from policy development and risk assessment to training, incident investigation, and continuous improvement, all aimed at creating a safe and healthy working environment.
Health and Safety Management services in the mining industry aim to prevent accidents, injuries, and occupational illnesses by implementing comprehensive policies, risk assessments, and safety programs. These services include regular training, incident reporting, and emergency preparedness to ensure a safe working environment. Continuous monitoring, audits, and community engagement further enhance safety and compliance with regulations.
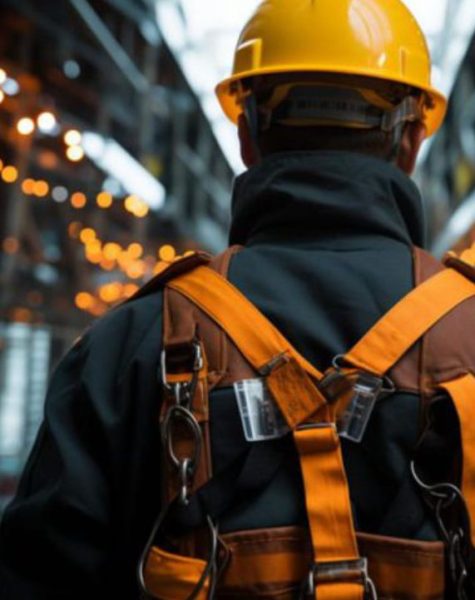
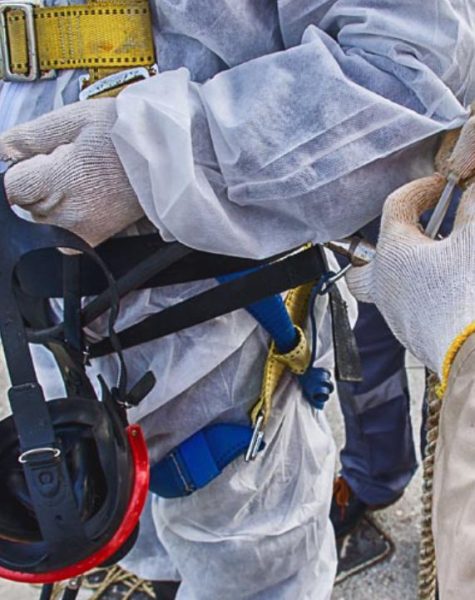
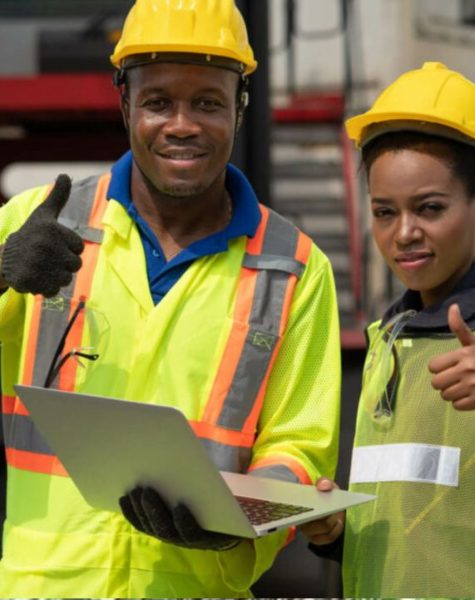
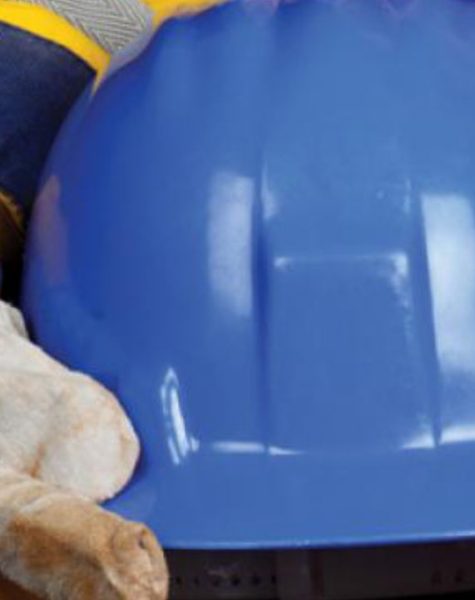
At Kelechi Minerals Nigeria Limited, we prioritize your safety with our comprehensive Health and Safety Management services, ensuring rigorous compliance with international standards. Our dedicated team conducts regular training, risk assessments, and audits to maintain the highest safety protocols. You can trust us to create a safe and healthy environment for all stakeholders, fostering a culture of safety and continuous improvement.
Kelechi Minerals Nigeria Ltd's Health and Safety Management services provide robust support to customers by ensuring a secure and compliant working environment through rigorous safety protocols and continuous monitoring. Our dedicated team works closely with customers to address safety concerns promptly, enhancing overall operational efficiency and well-being.
At Kelechi Minerals Nigeria Ltd, we guarantee top-tier Health and Safety Management services that adhere to international standards, ensuring the utmost safety for all stakeholders. Our commitment to continuous improvement and stringent safety protocols assures a secure and compliant working environment for your operations.
Community Engagement and Development
Geological Surveys and Mapping
Contact
- Plot 4 & 6 Jadesola Fadera Street, Akobo, Oyo State, Nigeria
-
+2349134024916
+2347037069243 - info@kelechimineralsltd.com
Brochures
View our corporate profile for an easy to read guide on all of the services offer.